The Evolution of Decontamination Technology
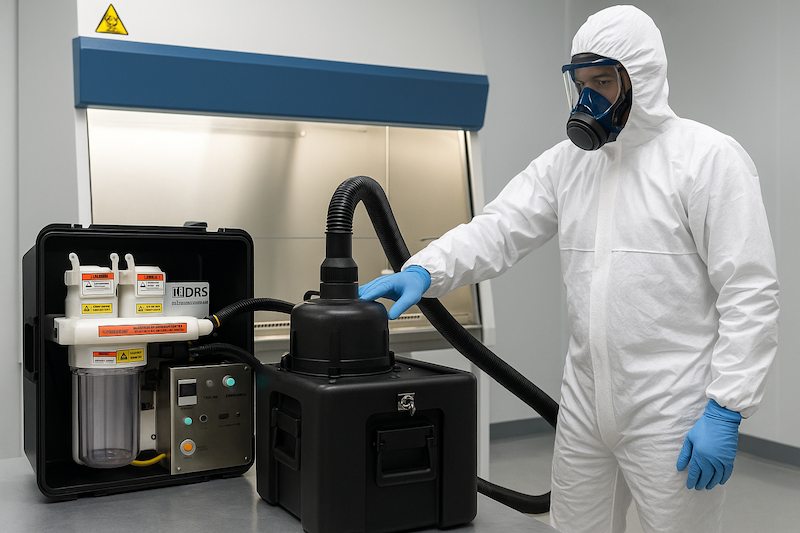
Executive Summary
In today's high-stakes Life Sciences environment, maintaining impeccable standards of cleanliness and safety is non-negotiable. Contamination can compromise research integrity, endanger personnel, and result in costly downtime. Quantus has established itself as an industry leader by implementing advanced chlorine dioxide (ClO₂) decontamination technology through a strategic partnership with DRS. By adopting the innovative DRS Mini Chlorine Dioxide System (MCS), Quantus demonstrates our commitment to continuous improvement in safety and efficiency for both our employees and clients. This article explores how our approach sets a new industry standard for effectiveness, safety, and efficiency, providing our clients with unmatched decontamination services that protect both assets and people.
The Evolution of Decontamination Technology
Traditional Decontamination Approaches
The Life Sciences industry has historically relied on several decontamination methods, with paraformaldehyde and vaporized hydrogen peroxide (VHP) being among the most common. While effective under specific conditions, these traditional methods have certain operational considerations that have prompted Quantus to explore alternative technologies:
Operational Considerations of Traditional Methods
Both paraformaldehyde and VHP decontamination methods have served the industry for many years, but present operational challenges:
- Extended Decontamination Times: Traditional decontamination cycles can require 10-17 hours from start to finish, creating significant equipment downtime.
- Process Complexity: Many traditional methods require additional neutralization steps that add time and complexity to the decontamination process.
- Distribution Challenges: Achieving consistent distribution throughout containment devices and reaching all surfaces can be challenging with some traditional methods.
- Material Compatibility Considerations: Some traditional decontaminants may have compatibility limitations with certain materials or may require specific contact parameters to be effective.
- Regulatory Requirements: All decontamination methods must adhere to strict regulatory guidelines that govern their application, documentation, and safety protocols.
The Life Sciences industry continually seeks more efficient alternatives that maintain or improve upon effectiveness while addressing these operational considerations. This drive for improvement led Quantus to investigate and ultimately adopt chlorine dioxide gas technology.
The Chlorine Dioxide Advantage
Chlorine dioxide (ClO₂) is a potent biocide known for its exceptional disinfection capabilities. Unlike some traditional disinfectants, ClO₂ is effective over a broad pH range and does not react with organic matter to form harmful by-products, making it an ideal choice for applications where safety and efficacy are paramount.
Scientific research consistently supports chlorine dioxide as a safe and efficient disinfectant. Studies have shown it effectively kills microorganisms even at concentrations as low as 20 to 30 mg/L, making it both powerful and economical.
Safety Profile of Chlorine Dioxide
When considering chlorine dioxide for decontamination purposes, several safety features stand out:
- Established Safety Parameters: The OSHA permissible exposure limit (PEL) for chlorine dioxide is 0.1 ppm as an 8-hour time-weighted average, providing clear safety guidelines.
- Residue Considerations: Chlorine dioxide decomposes to salt and water, leaving minimal residue on surfaces after treatment.
- Process Monitoring: The distinctive yellow-green color of chlorine dioxide allows for visual and spectrophotometric monitoring, enabling better process control.
- Environmental Profile: Chlorine dioxide breaks down readily in the environment, minimizing long-term environmental impact.
Operational Advantages of Chlorine Dioxide
Chlorine dioxide also offers significant practical advantages in decontamination applications:
- Significantly Reduced Cycle Times: While traditional decontamination methods typically require 10+ hours, chlorine dioxide decontamination using the DRS MCS system can be completed in less than 3½ hours.
- Minimal Residue: Chlorine dioxide leaves minimal residue on surfaces, eliminating the need for extensive post-treatment cleanup.
- Superior Distribution: As a true gas at room temperature, chlorine dioxide offers better distribution throughout spaces, reaching cracks, crevices, and difficult-to-access areas more effectively than many liquid-based disinfectants.
- Better Penetration: Chlorine dioxide gas can effectively penetrate through HEPA filters and into other challenging areas that liquid disinfectants cannot reach.
- Real-Time Monitoring: The distinctive yellow-green color of chlorine dioxide allows for direct visual and spectrophotometric monitoring, enabling better process control.
- Material Compatibility: Chlorine dioxide has demonstrated excellent compatibility with a wide range of materials, including electronics, without causing damage or accelerated degradation.
Quantus' Advanced Approach to Decontamination
The DRS Mini Chlorine Dioxide System (MCS)
At Quantus, we've made a strategic investment in advanced technology through our partnership with DRS. The DRS Mini Chlorine Dioxide System (MCS) represents our commitment to continuous improvement in decontamination practices.
This fully automated system (Patent No: US 8,524,167 B2) is designed specifically to:
- Maximize safety in biological safety cabinet decontamination
- Increase efficiency in laboratory equipment cleaning
- Provide superior results compared to traditional methods
With this innovative technology, we've achieved remarkable improvements in service delivery:
From 10+ hours to under 3½ hours total cycle time
This dramatic reduction enables same-day servicing, eliminating both extended equipment downtime and the need for additional service visits.
Key Benefits of Our Technology
Our implementation of the DRS MCS system offers several distinct advantages that set us apart in the industry:
- Enhanced Safety Profile: The MCS system includes multiple safety features and monitoring capabilities that protect both our technicians and your staff during the decontamination process.
- Unmatched Efficiency: The MCS system is built with a charcoal gas-scrubbing unit, allowing our trained technicians to safely remove chlorine dioxide gas after decontamination, requiring no external venting or chemical neutralization. This means faster turnaround and less disruption to your operations.
- Comprehensive Coverage: Our system circulates humidity and decontamination gas through both upstream and downstream exhaust HEPA filter plenums, eliminating the "dead leg" problem that plagues many biological safety cabinets. This ensures complete decontamination of all surfaces, including hard-to-reach areas.
- Material Compatibility: In testing and validation, chlorine dioxide gas has proven effective in decontaminating devices without material compatibility issues. This includes stainless steel, gasket material, internal paint, HEPA filter material, and materials involved with the BSC blowers. Even after multiple decontamination cycles, there are no deleterious effects on equipment functioning.
- Validated Effectiveness: Biological indicator validation demonstrates the effectiveness of our decontamination procedure, with proven reduction of 10^6 Bacillus atrophaeus spores. This provides documented evidence of sterilization-level decontamination.
How Quantus Raises the Bar: Our Enhanced Protocol
Secondary Containment for Added Safety
Quantus goes beyond standard protocols by using secondary containment methods, adding an extra layer of protection during the decontamination process. This ensures that any potential leaks during decontamination are safely contained, allowing your personnel to work safely nearby. This commitment to safety sets us apart from competitors who may not implement such rigorous precautions.
Comprehensive Process
Our decontamination process is meticulously designed to ensure maximum effectiveness:
- Thorough Preparation: We ensure all equipment is properly prepared and positioned for optimal gas circulation.
- Expert Application: Our certified technicians precisely control humidity levels and gas concentration throughout the process.
- Complete Verification: We use biological indicators and real-time monitoring to confirm successful decontamination.
- Safe Completion: Our gas scrubbing technology ensures all chlorine dioxide is safely removed before equipment is returned to service.
- Detailed Documentation: We provide comprehensive records of the entire process for your regulatory compliance needs.
Scientific Validation of Chlorine Dioxide Technology
Why Gas Decontamination Outperforms Liquid Disinfection
With the advantages of high efficacy, large disinfection volume, low corrosion, low hazard, and simple operation, gaseous disinfection has been shown to be a highly effective decontamination method. The scientific community continues to research and validate various decontamination approaches to determine best practices for different applications.
Studies comparing manual decontamination procedures to gaseous approaches have found gaseous decontamination to be not only more effective but also approximately 30% less costly than traditional spray-and-wipe methods. This represents significant operational savings while improving decontamination quality.
Comparative Analysis of Decontamination Methods
When comparing chlorine dioxide to paraformaldehyde and VHP for biological safety cabinet and room decontamination, several key differences become evident:
- Penetration Capabilities: Chlorine dioxide gas can effectively penetrate through HEPA filters without condensing along the path length, ensuring complete decontamination of critical filtration systems.
- Cycle Time Efficiency: Chlorine dioxide decontamination cycles typically complete in 3-4 hours, compared to 10+ hours for some traditional methods, significantly reducing equipment downtime.
- Temperature and Humidity Dependence: VHP requires precise control of relative humidity and temperature, while chlorine dioxide gas is less affected by temperature fluctuations, providing more consistent results across varied environmental conditions.
- Validation Approach: The physical properties of chlorine dioxide gas allow for easier cycle development and validation compared to some traditional decontamination methods, which may require extensive parameter adjustments for different spaces.
- Material Compatibility Profile: Each decontamination method has specific material compatibility considerations. Quantus has validated chlorine dioxide's compatibility with common laboratory materials through extensive testing.
Proven Microbiological Efficacy
Chlorine dioxide gas has been recognized as a broad spectrum, fast-acting oxidizing antimicrobial agent. It displays antimicrobial activity across a broad pH range and has little tendency to form organo-chlorine by-products.
In decontamination cycles, chlorine dioxide gas has been validated to achieve a 6-log reduction of bacterial spores at appropriate dosages, ensuring sterilization-level decontamination. This makes it ideal for critical applications where absolute cleanliness is essential.
Independent testing has confirmed the effectiveness of chlorine dioxide against a wide spectrum of pathogens, including bacteria, viruses, fungi, and bacterial spores. The gas has proven particularly effective against biological indicators using Bacillus atrophaeus and Geobacillus stearothermophilus, which are commonly used to validate sterilization processes.
Industry Applications and Benefits
Life Sciences Research and Manufacturing
For research laboratories and production facilities, our chlorine dioxide decontamination services provide several key benefits:
- Research Integrity: Eliminates cross-contamination concerns that could compromise experimental results.
- Operational Efficiency: Minimizes downtime with rapid decontamination processes.
- Regulatory Compliance: Meets stringent regulatory requirements for cleanliness and safety.
- Asset Protection: Safely decontaminates sensitive equipment without damage.
Healthcare and Pharmaceutical Settings
In healthcare and pharmaceutical environments, our services offer:
- Patient Safety: Eliminates pathogenic microorganisms that could endanger patients.
- Product Protection: Ensures sterile manufacturing environments for pharmaceutical products.
- Equipment Longevity: Provides effective decontamination without harsh chemicals that could damage equipment.
Environmental and Safety Considerations
Environmental Impact
The use of chlorine dioxide minimizes the amount of organochlorine compounds produced compared to traditional chlorine-based disinfectants. This makes it a more environmentally responsible choice for organizations committed to sustainable practices.
Chlorine dioxide breaks down more readily and generally has a lower environmental footprint. This reduced environmental impact aligns with modern sustainability goals and corporate environmental responsibility initiatives.
Occupational Safety Advantages
Comprehensive Exposure Management
Worker safety is paramount in any decontamination process. Quantus has developed comprehensive protocols to ensure safe implementation of chlorine dioxide technology:
Safety Parameters for Chlorine Dioxide:
- The OSHA permissible exposure limit (PEL) for chlorine dioxide is 0.1 ppm as an 8-hour time-weighted average
- Our processes include comprehensive safety measures to ensure exposure limits are never exceeded
- Our technicians use sophisticated monitoring equipment to verify safe conditions throughout the decontamination process
- The built-in charcoal scrubbing unit safely removes chlorine dioxide gas after decontamination
Comprehensive Risk Management
Quantus implements a comprehensive risk management approach with our chlorine dioxide decontamination services:
- Rigorous Training: All technicians receive specialized training in the safe handling and application of chlorine dioxide gas.
- Real-Time Monitoring: The visible nature of chlorine dioxide gas allows for visual confirmation of containment, while electronic monitors provide precise concentration measurements.
- Secondary Containment: Our enhanced protocols employ secondary containment methods that add an extra layer of protection against potential leaks.
- Complete Documentation: Detailed safety records and process documentation ensure regulatory compliance and provide a clear audit trail.
These safety protocols represent Quantus's commitment to protecting both your staff and our technicians while delivering superior decontamination results.
Economic and Operational Advantages
Cost-Effectiveness Analysis
Case studies have shown that chlorine dioxide gas decontamination can be approximately 30% less expensive than traditional manual cleaning and disinfection processes. This cost advantage comes from several factors:
- Reduced Labor Requirements: The automated process requires less hands-on time from technicians.
- Shorter Downtime: Faster cycle times mean less operational disruption and associated costs.
- Fewer Re-treatments: The comprehensive coverage ensures first-time success, eliminating the need for repeat decontaminations.
- Equipment Preservation: Less aggressive chemistry extends the lifespan of expensive laboratory equipment.
Operational Efficiency Improvements
Implementing chlorine dioxide in decontamination processes leads to significant efficiency improvements. Its high reactivity allows for lower dosages and shorter contact times compared to other disinfectants. These efficiencies translate to tangible benefits for our clients:
- Same-Day Service: Equipment can often be decontaminated and returned to service within the same working day.
- Predictable Scheduling: Consistent decontamination times allow for more precise maintenance scheduling.
- Reduced Personnel Exposure: The automated process minimizes staff exposure to potentially hazardous situations.
Key Takeaways
- Enhanced Safety Profile: Quantus's partnership with DRS demonstrates our commitment to implementing the safest available decontamination technology for both our technicians and your staff.
- Dramatically Reduced Downtime: Cutting decontamination cycles from 10+ hours to under 3½ hours significantly improves operational efficiency.
- Superior Effectiveness: Better penetration into difficult-to-reach areas ensures more complete decontamination than traditional methods.
- Lower Total Cost: 30% cost reduction compared to traditional methods when considering all factors including labor, downtime, and materials.
Ready to Upgrade Your Decontamination Approach?
Whether you need professional decontamination services or expert consulting for life sciences applications, we're here to help ensure your facility meets the highest safety standards.
Schedule Service Request Consultation